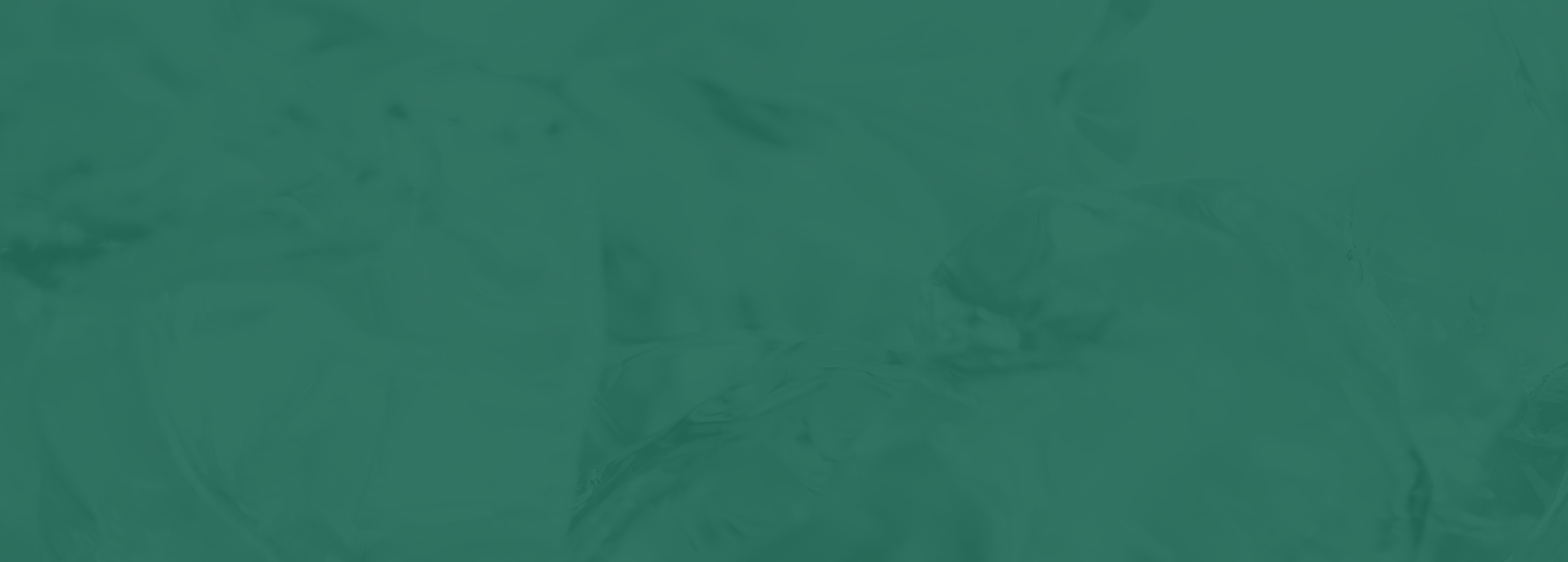
Paints & Coatings NASA
Challenge
Since 1958, NASA (National Aeronautics and Space Administration) has pioneered the quest to go beyond our physical limits, to test the scientific boundaries of space and technological boundaries developed on earth. One of NASA’s main programs, the Space Transportation System (STS), more commonly referred to as the Space Shuttle program, was first launched in 1981 and has undergone 122 missions at an average cost of $450 million per launch, according to NASA. The cost and worldwide attention given to each mission put extreme pressure on every component and system used for every flight.
Each shuttle produced by NASA is designed for a projected lifespan of 100 launches or ten years’ operational life. The STS program has been groundbreaking in its ability to accommodate commercial and classified satellites, astronauts, and service parts for the International Space Station. Each shuttle is composed of three main assemblies: the Orbiter Vehicle (OV), the rusted-color External Tank (ET), and two Reusable Solid Rocket Motors (RSRM), which propel the shuttle to space.
In 1998, through a $2.4 billion contract with ATK Thiokol, NASA extended the RSRM program for the production and refurbishment of 70 Reusable Solid Rocket Motors of the Space Shuttle Program. The extension is the sixth in a series of contracts, since 1973, for the design, development, production, and refurbishment of Solid Rocket Motors for the Space Shuttle Program and represents a continuing relationship between NASA’s Marshall Space Flight Center in Huntsville, Ala., and ATK Thiokol. The current RSRM is the largest solid motor ever flown and the first developed for reuse.
Three Space Shuttle main engines and the two RSRM provide 80% of the lift and enough thrust to elevate the 4.5 million pound shuttle into orbit during liftoff. Each RSRM is nearly the same height as the Statue of Liberty but weighs almost three times as much. The thrust produced from the 3 million pounds of propellant accelerates the Space Shuttle to a speed of more than 17,000 mph within the first eight minutes of launch.
After the boosters separate from the Shuttle’s Orbiter Vehicle and land in the ocean, they are recovered and disassembled. At the same time, the motors are returned to ATK Thiokol to begin refurbishment for the next NASA mission. Every facet of the Space Shuttle process must work in unison flawlessly, from the exterior paint to the solid fuel propellant. ATK Thiokol and all its partners are committed to creating the most efficient product in the future.
Solution
In 2005, ATK Thiokol chose CDF Corporation’s 5, 12, 30, and 55-gallon drum and pail liners for use in the first step of preparing primer and topcoat paint to the exterior of the RSRM hardware. CDF’s product quality, according to ATK Thiokol, “prevents transferable contamination from pail liner to paint or adhesive which may have a significant negative impact on RSRM quality and performance.”
Each motor consists of four segments, with the forward segment holding the igniter. In the production of each motor, ATK Thiokol determined CDF Corporation’s pail liners “provided superior performance for a critical application.” The great attention ensures the hardware’s integrity to quality and performance during production, inspection, transportation, and storage of motor components.
In addition to CDF Corp.’s product use in preparing the primer and topcoat paint for the exterior RSRM hardware, CDF’s pail liners were used to prepare an adhesive Chemlok© before application.
The external RSRM hardware is painted to protect against corrosion, and the internal diameter of the RSRM hardware is Chemlok© coated to form a bonding surface between the steel components and the insulation. Guaranteeing the purity and maximum performance of the materials was essential to the ATK Thiokol team as they highlighted CDF’s “attention to detail and focus on quality” as contributing factors to their joint venture. Assuring quality products and finishes is imperative to the overall success of every mission.
Results
CDF’s liners were chosen over competitive products after rigorous material and compatibility superiority testing. “Because we work closely with NASA to build a quality product for safe space missions, we have a rigorous qualification process for the products we use within the RSRM program,” stated ATK Thiokol Program Manager Jeff Champneys, who took a lead role in the ATK-CDF partnership. “CDF was one of few companies whose product satisfied all of the exacting RSRM requirements.” “For specific Reusable Solid Rocket Motor (RSRM) applications,” Champneys continues, “CDF provided the best quality product at the most competitive price.”
Get In Touch
We’d love to hear how we can work with your company to develop solutions, field your questions, or meet inspiring people like you to join our team.