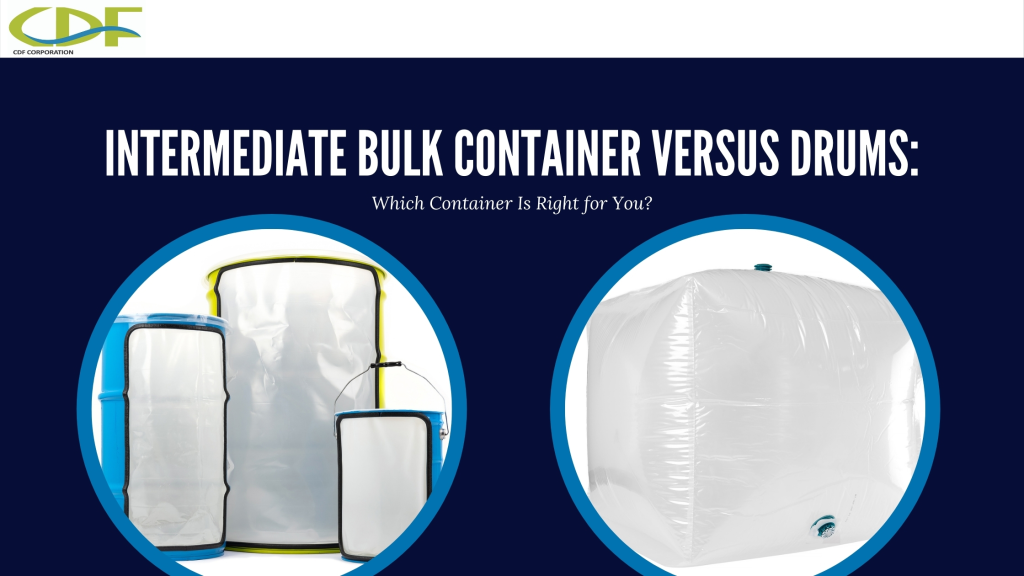
Pros and Cons of IBC Packaging Choices
Getting the best ROI while transporting your product depends on a lot of factors: the cost of manufacturing, the cost of packing, transport, and even storage viability. One of the largest costs, however, is tied up in one crucial aspect of the process: finding containers. The right containers can save your company money at nearly every stage: they’ll be easier to load, lighter to transport, safer to store. So which style is the right choice: drums, rigid bottle-and-cage intermediate bulk container (IBC) totes, or filled IBC liners? The answer may surprise you if you haven’t taken advantage of it yet.
IBC Drums: The Pros and Cons
Drums, typically made of either metal or plastic, have long been a stand-by for a variety of industries. Until innovation started making headway in other options, they weren’t a bad choice, as they were stable, strong, and predictable in size and weight. The problem is that use issues arose: it’s very difficult, for example, to get all of a liquid or viscous product removed from a drum, even with a gravity-assist dispenser. That leads to product waste, which in turn drives up costs. Drums pose an issue with storage, as their shape demands null space between rows—they take up more room in transport and storage than squared-off options. Finally, drums typically need to be thoroughly cleaned for sanitary or safety reasons, and that means paying for workers, cleaning materials, and time to do so between fillings and deliveries.
IBC Rigid Bottle and Cage: The Pros and Cons
Rigid bottle-and-cage IBC totes came along, eliminating that null space problem between rows of containers, but introducing new challenges in the process. The need to manufacture them with two different materials—one for the container and another for the cage—meant that the cost-per climbed upwards, negating many of the financial gains that changing shape offered. These bulk intermediate container types also have the same issues with cleaning routines: in fact, due to their shape, they can be even harder to clean than drums.
IBC Totes with Liners – The Pros and Cons
Arguably the best choice for shipping, storage, and dispensing today, the tote-liner IBC system provides versatility, makes the best use of space and weight, and doesn’t require the exhaustive cleaning process demanded by other IBC types. Liners make swapping out totes simple, and keep contents sealed and sanitary—a particularly important benefit for the food and beverage industry. Liners also work well with a wide variety of dispensing mechanisms, such as air-assist liners that deliver better product yield during dispensing, and cost up to 25% less in freight by allowing more volume usage. Form-fit liners work seamlessly—literally—during high-speed or difficult fills, and pillow liners keep out oxygen for aseptic-requirement products.
Choose the Right IBC for Your Needs
Selecting the right container option for your company will translate to cost savings during your manufacturing and shipping process, less effort wasted on leakage or contamination problems, and better ease-of-use for your end customers. While switching to a new type of container may seem challenging in your current workflow, the effort is well worth it, and will help improve your process from fill to sale and throughout the supply chain.
If you’re working with liquid and viscous products, make sure you’re getting everything you can from every intermediate bulk container, regardless of contents or size. Use the tools you already have at your warehouse’s disposal in a smart, revolutionary way—all while freeing up your employees to do important work elsewhere on the floor.
Learn what CDF’s Air-Assist liners can do for your company today!